
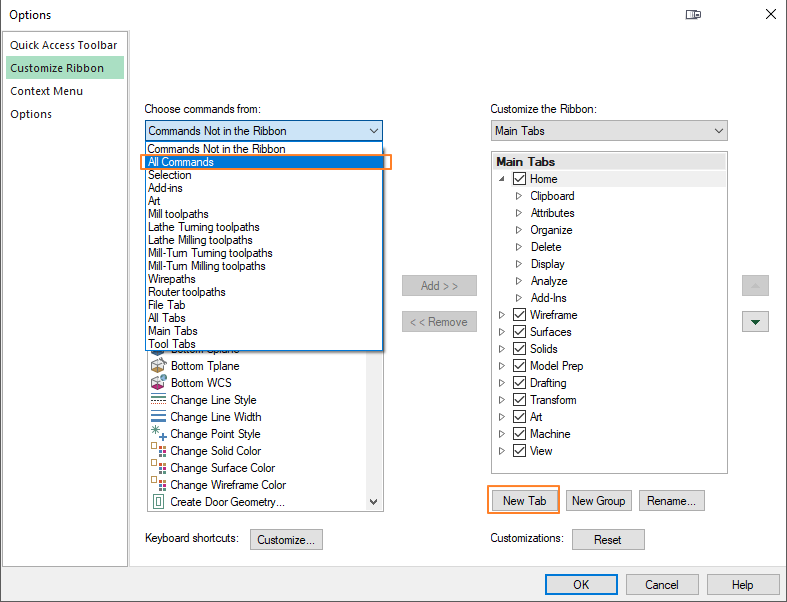
With G05.1 function turned on, the alternate directional program actually took 7secs longer, than with it turned off. This clearly indicates that the same Acceleration/Deceleration profile existed whether the small moves were in the same or opposing direction. With the G05.1 turned off, the alternate direction program cycle time was exactly (2min 40 sec) the same as the mono directional program. In this case there was no opportunity for the AICC function to optimize the Acceleration/Deceleration, and accordingly the programmed feed rate of F1000 was not achieved. Part of the test I did with the 18i, was to run another program also containing 20,000 0.05mm moves, but with each alternate block in the opposite direction of the one preceding it. With anything that reverses direction completely, ie the piston in a car engine, the item must come to a complete stop, then accelerate up to speed again. Without it, or with the function turned off the machine won't achieve high feed rates when the program is created with many very small moves to generate the shape. The max speed of the car will not be reached.ĪICC is a Fanuc Acceleration/Deceleration optimizing function, turned on and off by programming G05.1. Like accelerating a car as hard as possible and then decelerating to stop all within 50 meters. Every move the machine makes involves Acceleration/Deceleration, and if the moves are small, typical of a 3D program, then there will probably be insufficient distance in the move for the machine to achieve the program feed rate. Thanks Bill for for sharing you knowledge.īut I still don't get it, do you suggest that there's something wrong in our machine settings (parameter) the way it Accelerate/Decelerate?

See the other thread for a more detailed explanation. With AICC turned on, the feed was steady at F1000 and the cycle time was 1min on the dot. With the function turned off, and using F1000 feed as the benchmark, the actual feed maxed out at F375, with a 2min 40 sec cycle time. I recently did tests on a Fanuc 18i with the AICC function using a program that had 20,000 0.05mm moves (1,000mm total travel). But I believe you will find that the issue is Acceleration/Deceleration related, not data transfer. That is, if the following X coordinate is the same as the one preceding it, don't have that output in your program. To ensure that the greatest amount of useful data is arriving at the machine, make sure that the program being sent consists of modal data only where required.
#MASTERCAM V9 CIMCO DOWN PLUS#
This subject was covered at length in a previous thread only in the last week or so in this forum.Ĥ800 baud is relatively slow by today's standards, but even at that speed, and forgetting about Stop and Parity bits, there would be approx 600 characters per second arriving at the machine, plus you have a buffer in the machine's Uart. That being the case, the issue is caused by there not being enough distance in each move for the slides to accelerate to the programmed feed, before having to decelerate. It also happen in my Robodrill w/ a 9600 baud rate it also run out of data bcoz of higher feedrate.Dont know why.You state that it only happens during 3D machining, so I assume that the moves to generate the shape are quite small.

During transmission the machine can only handle 72character/sec thats why the actual feedrate drop because it runs out of data being only happens during 3D machining. My Mori had a 4800 baud rate.i think the machine cannot compensate every data character/second being transmitted by the DNC because its baud rate is just small.
